
Engineering Inspections
Alan Boswell Risk Management can help ensure you meet your legal obligations when it comes to examination of your equipment and machinery.
- Ensuring compliance with legislation
- Full documentation of inspections
- Annual contract
- Competitive pricing


Certain types of plant and equipment require mandatory engineering inspections on a regular basis. In order to ensure the safety of everyone involved with the equipment, these inspections must be carried out by a qualified person.
Typical examples of plant and machinery required to be inspected are lifts, compressors, or plant fitted with hydraulics, chains, wires, or ropes. Also, any mechanical extraction system used to control hazardous substances.
Alan Boswell Group can provide all the inspection services and support you need.
The Alan Boswell Group Difference
Engineering inspection is an area often overlooked by businesses in the UK, but we can help. Our in-house Engineer Surveyors will work with you to identify which items of your work equipment require inspections and establish how frequently these checks are required. We will also carry out the appropriate inspections, ensuring you meet your legal requirements.

Engineering inspections in detail
Insurance experts
Inspections
Ongoing inspection
Paperwork
Failure to have items of your plant and equipment checked means any potential liability claims may not be covered by your insurance. This can also lead to prosecutions. It is vital to seek professional guidance about your obligations. Find out more on legal requirements for your equipment and best practice for regular inspections.
FAQs
Get in touch
To talk through your risk management, health and safety, or training requirements, get in touch with a member of our team today.
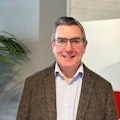
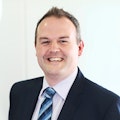