Prevention not reaction: how regular engineering inspections keep your farm and workers safe
UK farms are a surprisingly deadly environment in which to work.
By Alan Boswell Group
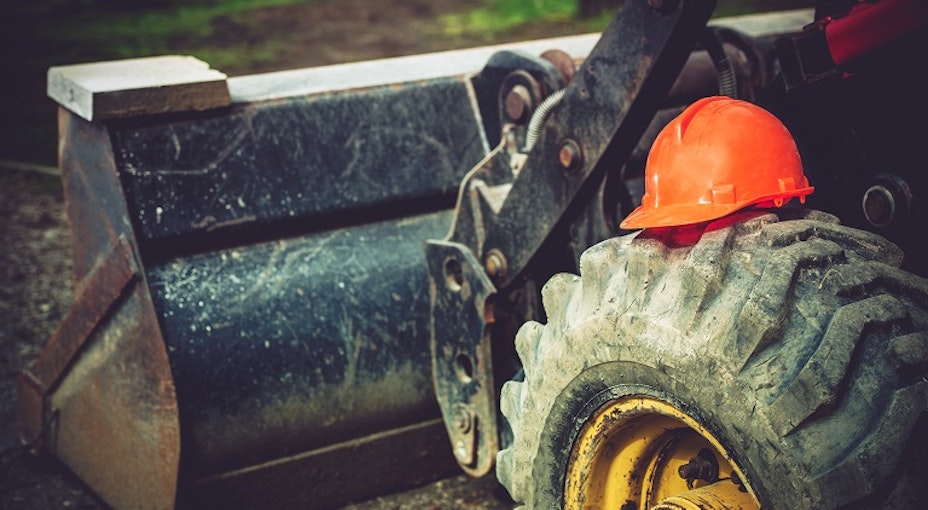
According to data released in 2020 by the Health and Safety Executive (HSE), workers in the agriculture, forestry and fishing sector are around 18 times more likely to be killed at work than the average for all other sectors combined.
In response to these findings, the HSE and insurance underwriters are putting increasing emphasis on the value of on-farm checks of equipment. Regular engineering inspections can help you find risks early, stopping accidents before they happen.
Not only this, but some of these checks are required by law. Failure to arrange them could result in you being served with an improvement or prohibition notice. In severe cases, you could be prosecuted.
Simon Wyeld, Lead Engineer at Alan Boswell Risk Management (ABRM), explains what your legal responsibilities are, why it’s important to stick to an inspection schedule and how the team at ABRM can help keep you and your farm safe.
What are LOLER regulations and what do farmers need to do?
"If your business owns or operates lifting equipment in any capacity, it must comply with the Lifting Operations and Lifting Equipment Regulations 1988 (LOLER). These are in place to ensure that all lifting equipment is safe to use."
LOLER inspections must be carried out by a ‘competent person’ which means someone who is qualified – usually an engineer. This person will have practical knowledge and experience of the lifting equipment and so can spot any weaknesses or defects that you might miss in the day-to-day running of the farm."
After the inspection, you’ll receive a report which contains information required by LOLER Schedule 1, including:
The examination date
The date when the next thorough examination is due
Any defects found which are (or could potentially become) a danger to people.
You have to keep the records from each inspection, and you need to make sure the equipment is appropriately marked to show it’s been tested. If a serious defect is found, this has to be verbally reported to the person in charge of the equipment and then followed up by a written report. Whoever completes the inspection has a legal requirement to notify the HSE of serious defects."
Why are inspections important?
"People view LOLER inspections as a bit of a thorn in the side – there’s this idea that health and safety is all about busybodies coming in and telling you everything that’s wrong. Inspections can be used as a really useful tool though and, more importantly, they keep you on the right side of the law. They keep your insurers happy too! There’s a danger that, without proof of a machine’s safety, your insurance could be invalidated."
In the event of an accident, farms that have their equipment inspected regularly and keep the documentation to prove its work-worthiness are more likely to avoid the cost and misery of fines and possible prosecution. Really, there’s no reason not to have regular inspections; you’ll get the most out of the investment you made in your farm equipment and you have peace of mind that your workers are safe."
What sort of defects do you find?
"The following pictures show two different but serious defects we’ve found on farms."
The first is a damaged lifting sling. You’ll find lifting slings on most farms and the one pictured has a safe working load of 1000kg. As lifting operations are often carried out in close proximity to people, there is a real risk of this sling breaking, causing serious or even fatal injuries. The good news is that lifting slings are relatively cheap and easy to replace, so the problem can be sorted quickly."
The next two pictures show the front axle to chassis anchorage bolts of a JCB telehandler. The bolts have come so loose that they could be rotated by hand. An immediate defect was issued – it would have been a journey to remember, driving down the road and suddenly the front axle falls off!"

What can farmers do to avoid serious defects?
"A LOLER inspection is not the same as routine maintenance, and it shouldn’t be viewed as such. Keeping your equipment in generally good condition, such as replacing worn or damaged parts, topping up fluid levels, or making minor adjustments can help not only keep your farm safe, but also save you money in the long run. After all, if an item is worn, it’s easier to repair it, rather than keep using it until it fails. At this point it may no longer financially viable to repair, or in the worst case, it fails and causes a serious or fatal accident.
"We always advise you have a routine maintenance program (and we can help you put one together if needed). Most manufacturers provide service intervals, so include these in your program and have guidelines to follow, such as
Pre-use checks
Daily checks
Monthly checks
Six-monthly checks
"It’s a huge help to us if you clean the item before inspection too! We understand these are busy working environments, but by putting routines in place you can almost forget about it as it becomes part of the daily running. The whole point is to be preventative and make the farm safe rather than be reactive and having to deal with the fallout from a potentially terrible accident."
What does Alan Boswell Risk Management bring?
"While we all take our role seriously and have a wealth of knowledge and industry experience, what sets us apart is our approach to inspections. We work with you, find the best time to visit to minimise disruption to the business, while still making sure the inspections are carried out by the due date.
"If we find a serious defect, whilst we are legally required to inform the HSE, we will also show you what we’ve found and talk you through what action needs to be taken. It’s not to scare you, more we want to make sure you understand what you need to do to make it safe."
We’re available for more than just site visits. If you have any questions or concerns you can call the office or engineers for advice. We’re here to take that worry away, minimise risk and prevent accidents. For me personally, having worked at a large engineering inspection company and seeing how they operate, it’s a refreshing change being part of the Alan Boswell Group where customer care and satisfaction is important."
Need help with your insurance?
Whether you need a quote, have a general enquiry, or want to talk it through over the phone, we're here to help.
Send an enquiry
Related guides and insights
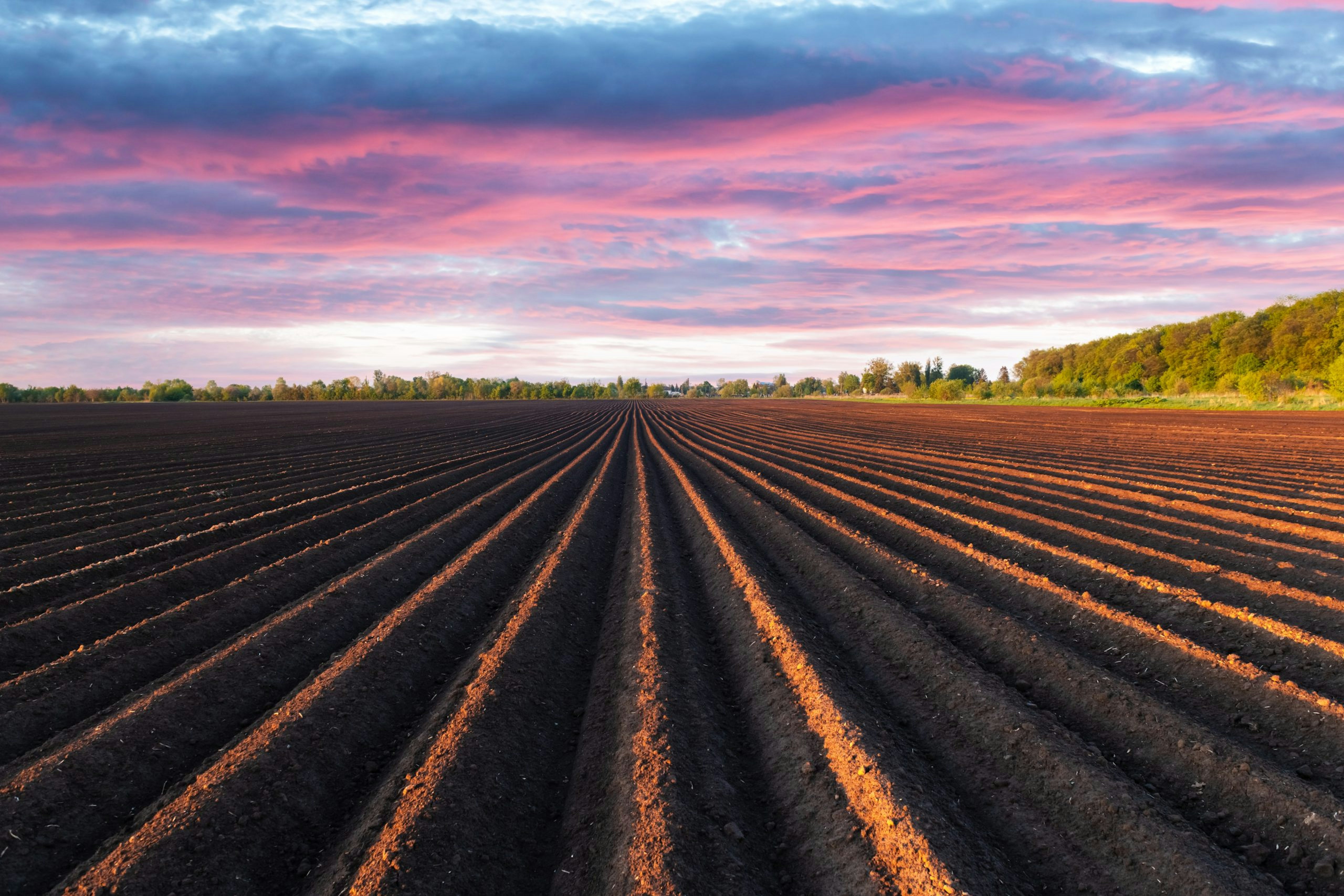
Types of farms in the UK
The agricultural sector is one of the UK’s major industries. It’s also a diverse one, covering everything from livestock and arable farming to market gardening. We take a look at the types of farm in the UK and the insurance they need.
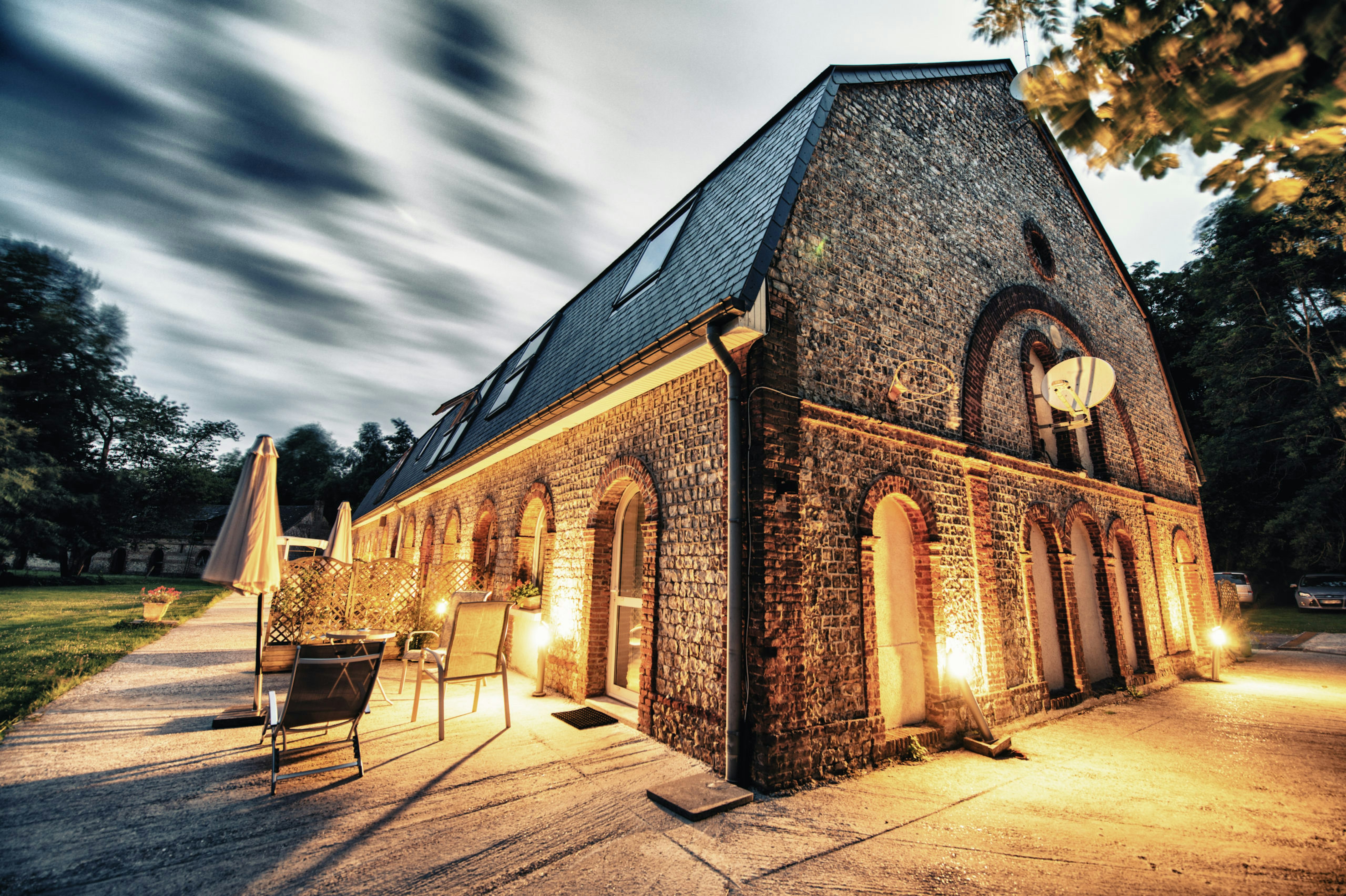
Top farm diversification ideas
Last year 68% of farms had chosen to diversify. We look at some the ways farmers are diversifying and the possible profits behind those ideas.
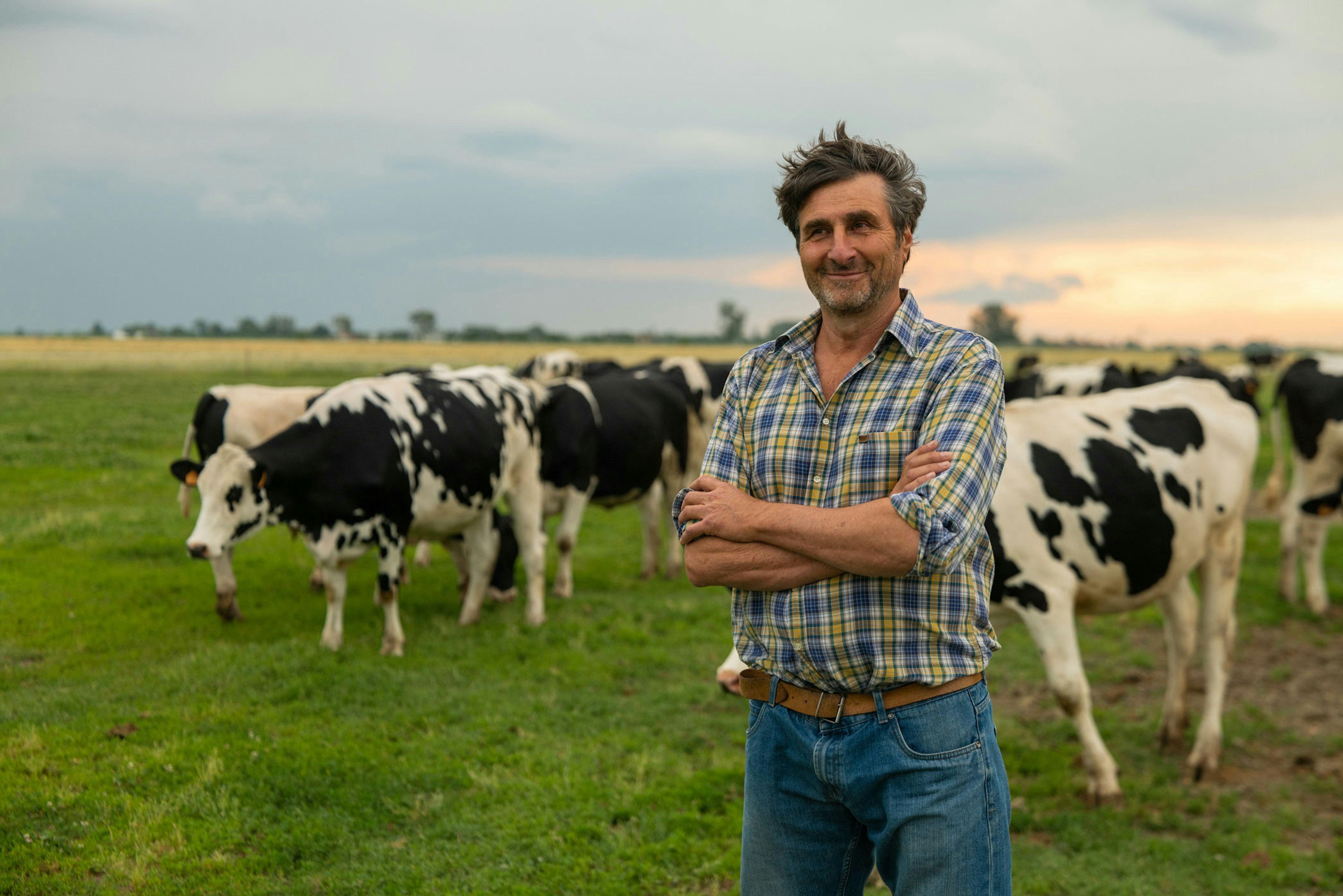
Guide to farm succession planning
The absence of succession planning can mean you’re unwittingly placing your farm business at financial risk. Here, we explore why farm succession planning is important and what you should consider when putting a plan together.