Guide to supply chain risk management and insurance
By Alan Boswell Group
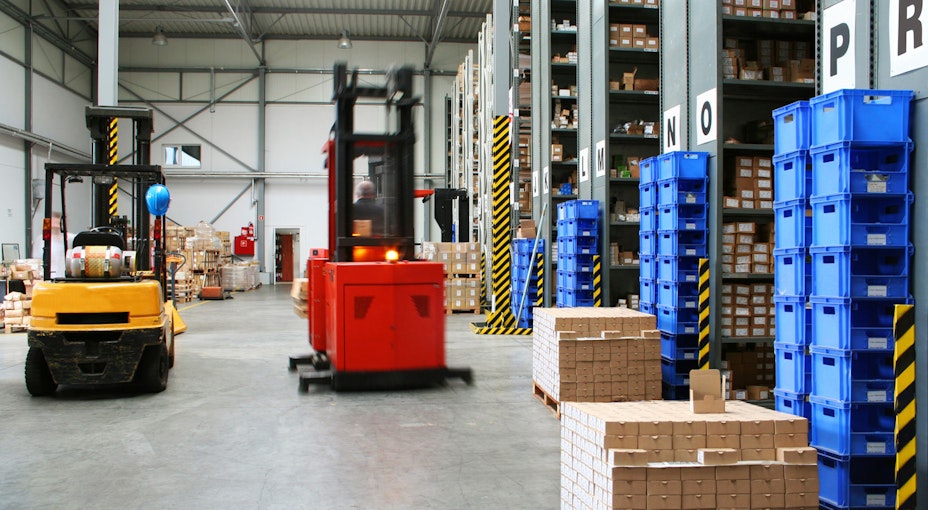
In this article
An organisation’s supply chain greases the wheels of its entire operation, and one broken cog can bring the whole thing grinding to a halt. In recent years, the eruption of an Icelandic volcano, a container ship stuck in a canal, the Covid-19 pandemic, and the fall-out from Brexit have all disrupted supply chains. But much less dramatic or globally visible issues can bite hard too, such as a fire at a supplier’s premises, a supplier suddenly going bust, or a disruption to a company’s own manufacturing processes. All of which explains why supply chain risk management has never been more important to the smooth running of a business. In this guide, we’ll explore the types of risk, the importance of supply chain risk management strategies, and how insurance can help to protect the smooth running of your business.
What is a supply chain risk?
The best way to limit the impact of supply chain disruptions to your business is to identify the risks within your supply chain. Only then can you develop strategies to mitigate their impacts. Supply chain risk factors are split between:
external risks, which are outside of your control;
internal risks, which are more within your control.
External supply chain risks
These are risks which originate from outside your organisation, including:
demand risks, caused by unpredictable customer demand and can be the result of a lack of insight into purchasing trends;
supply risks, caused by an interruption in the supply of materials or parts that your business relies on to operate;
environmental risks, the result of governmental, economic, societal or environmental issues that impact the supply chain;
business risks, caused by unexpected changes to a company in your supply chain that you rely on, such as financial instability, issues with their manufacturing plant, or a change of ownership.
Internal supply chain risks
Internal risks are more within your control and can therefore be more easily identified and monitored. That doesn’t mean they can always be avoided but, with good planning, you can mitigate against excessive disruption. Internal risks include:
manufacturing risks, resulting from disruptions to any part of your internal production processes, causing manufacturing downtime;
business risks, such as unexpected changes to key personnel, management, reporting structures or business processes;
planning and control risks, caused by inadequate or ineffective production planning and / or inaccurate forecasting;
mitigation and contingency risks, caused by not having a contingency plan in place if something goes wrong in your supply chain;
cultural risks, for example if there is a corporate culture to downplay negative information, the business may be slower to react to unexpected events.
Known risks can be monitored and mitigated against more easily. For example, if you know the risk of a failure in your manufacturing equipment, you can implement a robust plan to minimise the time your production capacity is diminished. Known risks can also include external risks. By monitoring the financial health of your suppliers using publicly available information, you may be able to anticipate and plan for potential issues in advance. Unknown risks are more difficult - or sometimes impossible - to predict. No-one could have foreseen the Icelandic volcanic eruption, for example, and the chaos caused by the subsequent ash cloud that led to the largest air-traffic shut-down since the second world war. The Covid-19 pandemic combined a sudden global health emergency with government-enforced lockdowns, highlighting the need more than ever for robust risk management as global supply chain risks increase.
Why is supply chain risk management important?
Events on the other side of the world can have a devastating impact on the most well-run business and, as we’ve seen, global health threats, the effects of climate change, natural disasters, and cybercrime can all have a far-reaching impact on supply chains. Business must now pay attention to the consequences of these emerging threats in addition to the more conventional supplier risks like bankruptcy and manufacturing disruption. Failure to properly assess and manage risks within your supply chain can leave your organisation wrong-footed and slow to react, resulting in significant manufacturing downtime, no product to sell, and no income stream.
How can you identify the supply chain risks in your business?
Effective supply chain risk mitigation relies on knowing, as far as possible, where the risks are in your business. The first step to identifying the risks in your supply chain is to map out and document your supply chain network for all your vital raw materials, parts or products. Listing all your suppliers and assessing where they are based, how the goods reach you, their financial history, and how vulnerable they are to political, economic or environmental threats will allow you to identify the most likely pinch points. The more information you have the better you can understand all parts of your supply chain. Identifying internal risks is largely a case of auditing every aspect of your own processes and recording everything that could possibly go wrong under the manufacturing, business, planning and contingency risk areas. Once you have identified the risks, record them on a risk register and score them based on:
the likelihood of the risk materialising;
its likely impact on the business if it does;
your organisation’s preparedness to deal with the risk should it materialise.
The register should be continuously monitored and updated for any changes.
What steps can you take to reduce supply chain risk?
You’ve now identified the supply chain risks your business may face, so what practical steps can you take to mitigate their effects? Here, we’ll look at some of the most common ways you can protect your business from supply chain shocks.
Move from single-source to multi-source model
The dangers of using a single source for products or materials was brought into sharp focus by the Covid-19 pandemic. Companies that used a single supplier in China, which saw a series of severe lockdowns in different cities from January 2020 onwards, were left scrambling for alternatives. It highlighted the importance of, where possible, sourcing materials from at least two different suppliers in different geographic areas. Using multiple suppliers provides a contingency in the event of a single company suffering an unforeseen event.
Try to find local suppliers
The more distance your product or material has to travel to you, the more likely it will be affected by global supply chain issues. Suppliers closer to home may be more expensive, but by shortening the travel time you can also reduce potential risks.
Store enough stock to cope with supply chain disruptions
Storing additional stock or raw materials can provide breathing space to help see you through any disruptions to supply, either temporary from your existing supplier or to give you time to find an alternative.
Consider dual premises and duplication of essential supplies
Holding key stock and essential materials on more than one site can prevent a total loss in the event of a major incident at one of your premises.
Formalise agreements with key suppliers
It’s advisable to formalise supply agreements with suppliers for critical items. Consideration should be given to penalty clauses for non-supply where vital to business continuity.
Ensure your suppliers have robust risk management plans
As part of supply chain due diligence, you should check that suppliers have disaster or business recovery plans. Such plans should be requested and checked for relevance, with evidence of regular reviews.
Try to reduce long lead times
Does your company use any essential materials on which there is a long lead, or delivery, time? If so, it is important these products are identified in the supply chain and arrangements put in place with alternative providers where possible. You should also explore possibilities for reducing particularly long lead times.
Audit the quality of goods and services provided by suppliers
A supply of sub-standard products can be just as damaging to your business as not receiving them at all. That’s why it’s important to put in place an ‘incoming quality audit’ procedure, with quality checks carried out by trained staff.
Improve your cyber supply chain risk management
Malware, ransomware, phishing, and hacking attacks have risen exponentially in recent years and pose a serious threat to your supply chain. Businesses should establish robust internal cyber security measures, and implement compliance standards for all suppliers and distributors.
Assess prospective suppliers’ financial stability
Before agreeing a contract with a new supplier, consider using a credit rating agency to provide a predictive financial stability report.
Foster a culture of risk awareness
Carry out risk awareness training across all levels of your business, covering at least the basics of supply chain risk, best practice, and cybersecurity.
The importance of contingency plans
Every organisation needs to have contingency plans in place to best ensure business continuity in the event of a disruption to normal operations. This applies to any type of disruptive crisis, including problems in the supply chain, and is vital to restoring full productivity with minimal financial loss and/or damage to reputation and viability. A disaster recovery plan, or DR plan, is a document that lays out how you will protect your business in the wake of a catastrophic event. When it comes to supply chain disruption, the DR plan should detail a plan of action for every scenario envisaged by your detailed supply chain risk register. A team should be put in place to make critical decisions, as well as robust communication channels so that employees know what their responsibilities are in the event of supply chain disruption.
What insurance products are available for supply chain risks?
Even with the most rigorous supply chain risk management processes in place, sometimes disruption is inevitable. The importance of insurance in supply chain management, therefore, cannot be overstated. Principally, protection is provided by business interruption insurance, which provides cover for loss of income as a result of an unexpected incident which means that the business cannot operate as normal (usually arising from damage).For example, should there be a fire at a supplier’s premises, leading to a loss of critical parts required to keep your manufacturing plant operating, business interruption insurance should be able to help, if critical and dependant suppliers have been noted on the cover. The policy would aim to restore your business to the same position it was in prior to the loss, while also providing you with the funds to continue business as usual by paying wages, bills and maintaining profits. Meanwhile, goods in transit, marine/airfreight, and stock throughput insurance are all further ways to protect against supply chain exposure. Goods in transit covers the movement of goods you are responsible for within the UK, while marine/airfreight insurance normally refers to the overseas movement of goods. Stock throughput insurance is a useful option to cover stock through the whole supply chain, providing protection from the moment you purchase goods from a supplier, to storage at your own or a third party premises, through to final delivery to the end customer.
Outsourcing risk management
There may be occasions when businesses lack the in-house expertise to carry out a full risk management function. But areas like supply chain risk management, business continuity and environmental management are far too important to be left to chance. That’s why it can pay to outsource your risk management to qualified specialists. Alan Boswell Risk Management can provide a range of services to help you identify the main risks you face as a business, including potential problems in your supply chain. A business continuity survey will identify any weaknesses in your preparedness for an emergency, while ongoing training, guidance and advice will help you to build up a broader knowledge base within your organisation.
Get in touch
Whether you want to speak with one of our advisors or have a general enquiry, we're here to help.
Risk management enquiry
Related guides and insights
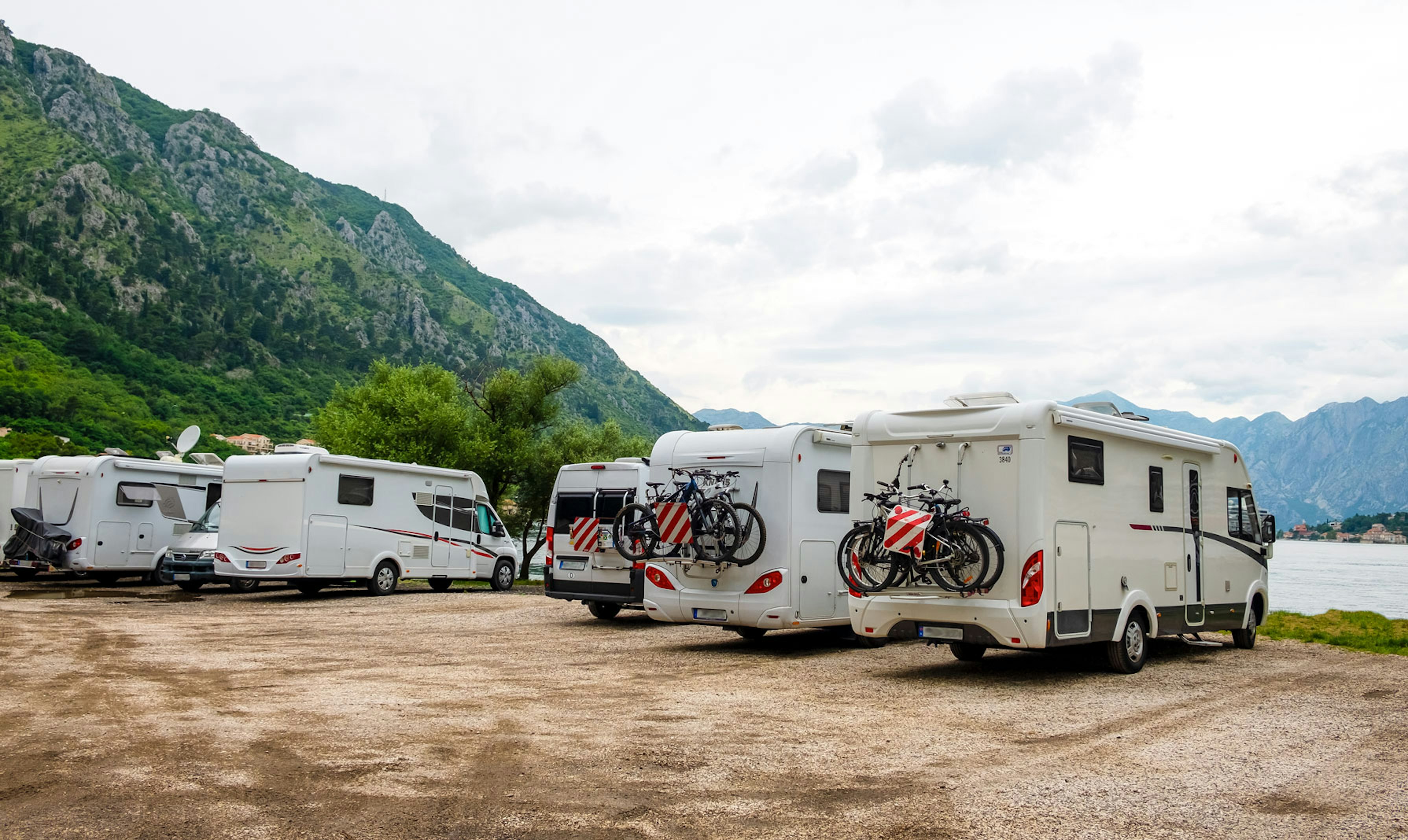
Risk management strategies for campervan and motorhome hire companies
As the popularity of campervan rentals continues to rise, so do the associated risks. Ensuring the safety and security of your vehicle and the renter is important when looking to maintain a successful and reputable rental business. In this context, implementing robust risk management strategies can help mitigate potential problems and protect your investment. This article outlines strategies to identify, assess, and mitigate risks associated with renting out your vehicle to customers.
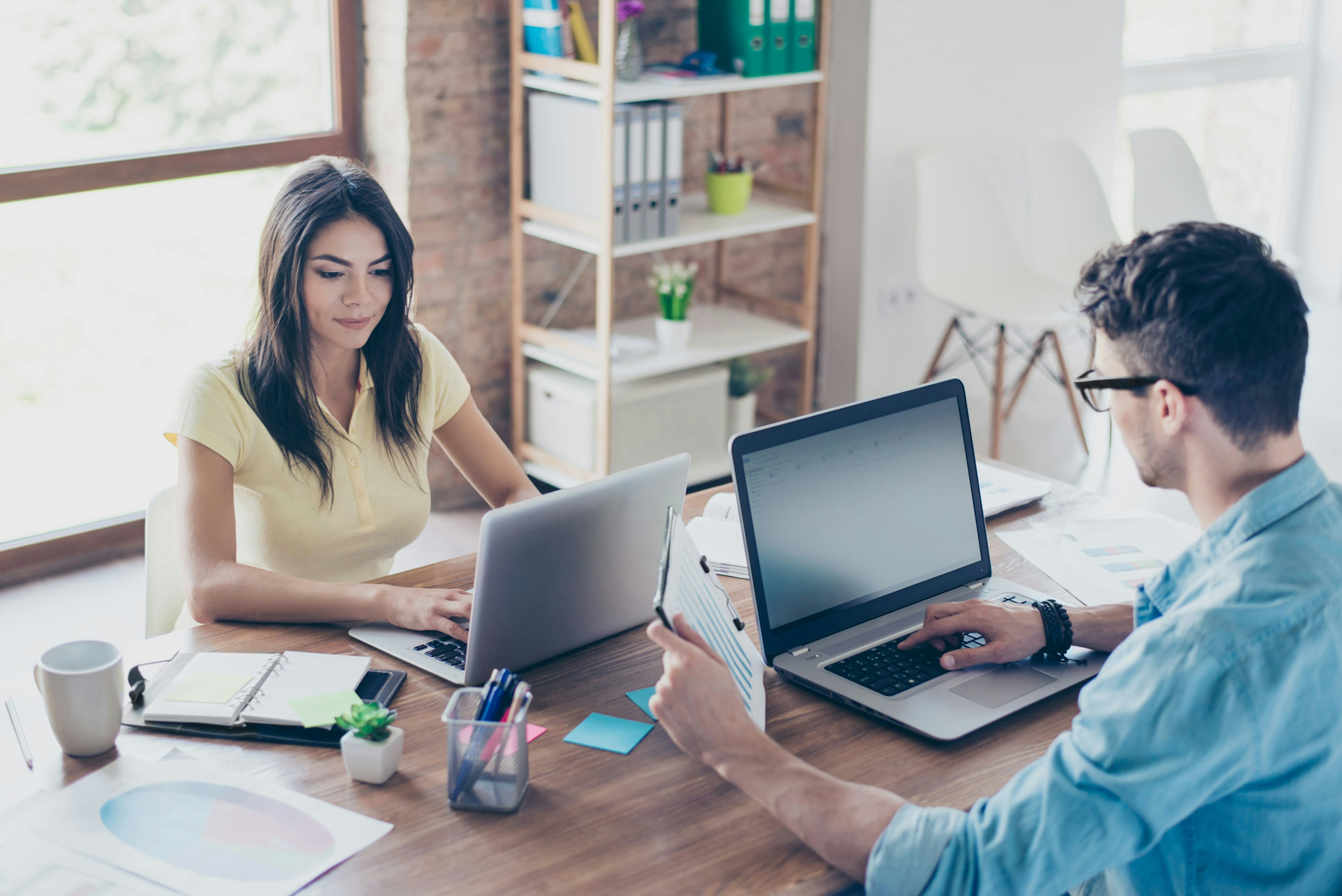
Guide to DSE risk assessments
No matter the industry you operate in or the size of your business, it is likely that your employees will use Display Screen Equipment, or DSE. In this guide, we share everything you need to know about DSE regulations.
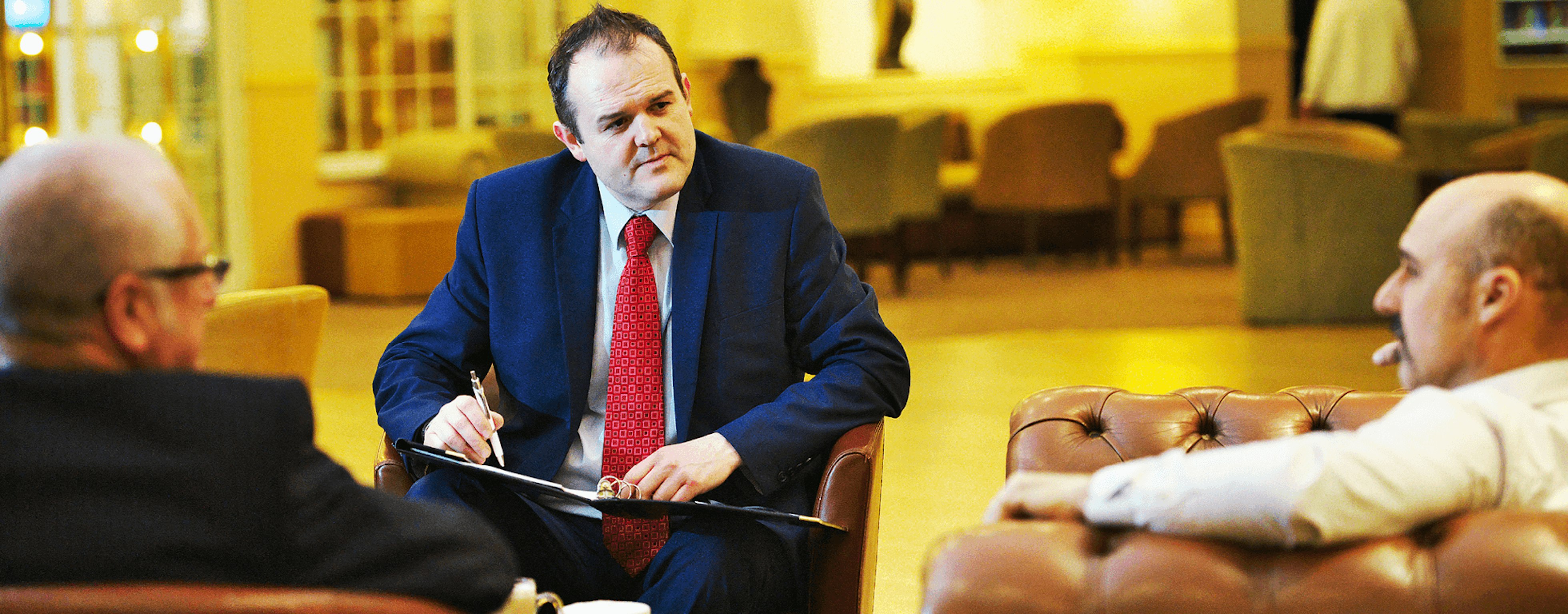
What is a risk assessment?
A good risk assessment can help you prepare for hazards and minimise the financial burden. Here’s why overlooking its importance can leave your business vulnerable.
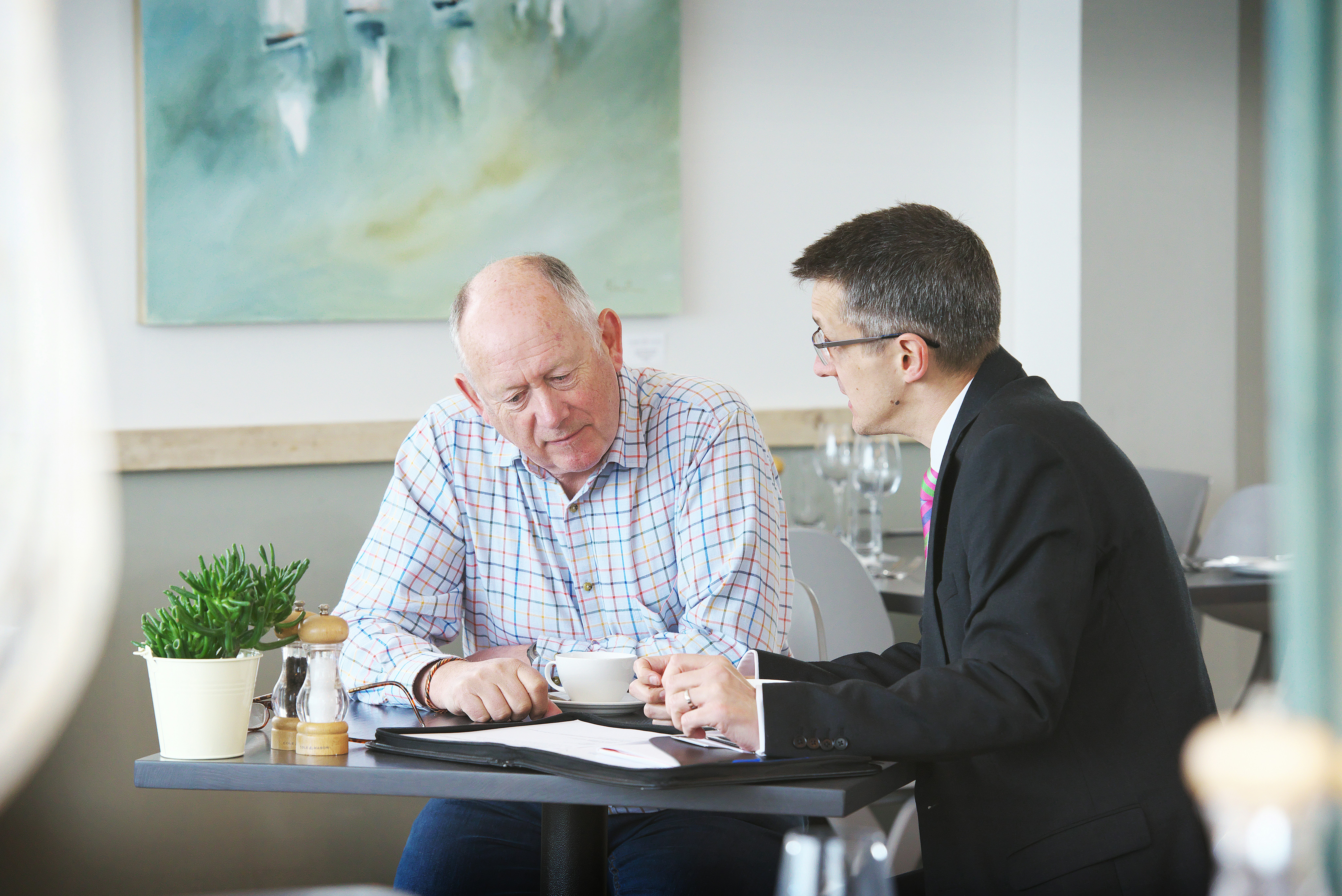
Why use an independent insurance broker?
Not sure why you should use an independent insurance broker over a price comparison site? Our latest post has all the answers.